Contact : +91-79045 61980 | Email: hydrofitengineers@gmail.com
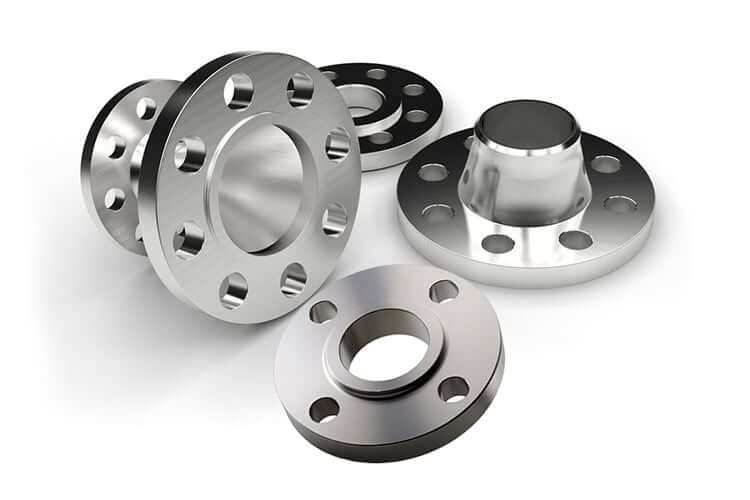
Stainless steel flanges are essential components in piping systems, providing a means for connecting pipes, valves, pumps, and other equipment. These flanges play a crucial role in facilitating assembly, disassembly, and maintenance of pipelines. Here are key aspects related to stainless steel flanges
Stainless Steel Types: Common stainless steel grades for flanges include 304, 316, 316L, and other variations. The choice of grade depends on factors such as corrosion resistance, temperature requirements, and the specific application
Types of Stainless Steel Flanges
There are several types of flanges, each designed for specific applications and requirements in piping systems. The choice of flange type depends on factors such as the pressure, temperature, material compatibility, and the purpose of the connection. Here are some common types of flanges:
- Weld Neck Flange (WN):
- Features a long neck that extends from the base and is welded to the pipe.
- Suitable for high-pressure and high-temperature applications.
- Provides structural reinforcement and helps prevent leakage.
- Slip-On Flange (SO):
- Slips over the pipe and is then welded in place at the backside.
- Ideal for low-pressure applications and easy to install.
- Used in applications where regular maintenance and inspection are required.
- Blind Flange (BL):
- Used to close the end of a pipe or vessel.
- Has no bore, making it suitable for applications where the end of the pipe needs to be sealed.
- Often used in pressure testing scenarios.
- Socket Weld Flange (SW):
- Welded directly onto the pipe.
- The socket provides a recess to hold the pipe, allowing for a smooth flow of fluid.
- Suitable for applications with lower pressures and temperatures.
- Threaded Flange (TH):
- Has internal threads and screws onto the pipe with external threads.
- Used in low-pressure, non-critical applications.
- Common in smaller pipe sizes.
- Lap Joint Flange (LJ):
- Consists of two parts: a stub end and a loose backing flange.
- The two components are connected with bolts.
- Allows for easy alignment and adjustment during installation.
- Orifice Flange:
- Specifically designed for use with orifice meters to measure the flow rate of fluids.
- Has a concentric hole to accommodate the orifice meter.
- Expander Flange:
- Used in applications where an increase in pipe size is required.
- The larger end of the flange accommodates the larger pipe, while the smaller end connects to the existing pipe.
- Reducing Flange:
- Connects pipes of different sizes.
- The flange has a larger bore on one side and a smaller bore on the other.
- Ring Type Joint Flange (RTJ):
- Features a groove to accommodate a metal ring gasket.
- Suitable for high-pressure and high-temperature applications.
- Commonly used in the oil and gas industry.
- Long Weld Neck Flange (LWN):
- Similar to weld neck flanges but with an extended neck.
- Provides additional reinforcement and is often used in high-pressure applications.
- Square Flange:
- Has a square shape rather than a circular one.
- Used in specialized applications where square-shaped connections are required.
- Spacer Flange:
- Used to increase the distance between two flanges in a piping system.
- Helpful in applications where additional space is needed.
These are just a few examples of the many types of flanges available. The selection of the appropriate flange type depends on the specific requirements of the piping system and the conditions under which it operates. Each type of flange serves a particular purpose, contributing to the overall functionality and reliability of the piping system.
There are several types of flanges, each designed for specific applications and requirements in piping systems. The choice of flange type depends on factors such as the pressure, temperature, material compatibility, and the purpose of the connection. Here are some common types of flanges:
Flange Faces
Weld Neck Flange
- Features a long neck that extends from the base and is welded to the pipe.
- Suitable for high-pressure and high-temperature applications.
- Provides structural reinforcement and helps prevent leakage.
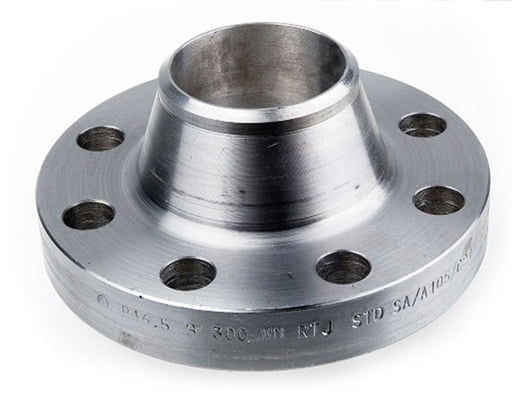
Slipon flange
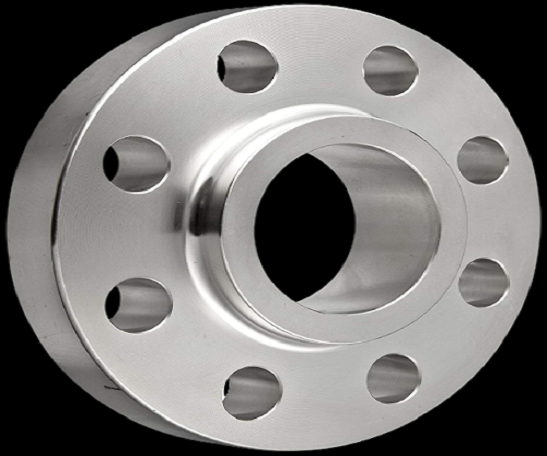
- Slips over the pipe and is then welded in place at the backside.
- Ideal for low-pressure applications and easy to install.
- Used in applications where regular maintenance and inspection are required.
Blind Flange
- Used to close the end of a pipe or vessel.
- Has no bore, making it suitable for applications where the end of the pipe needs to be sealed.
- Often used in pressure testing scenarios

Socket Weld Flange
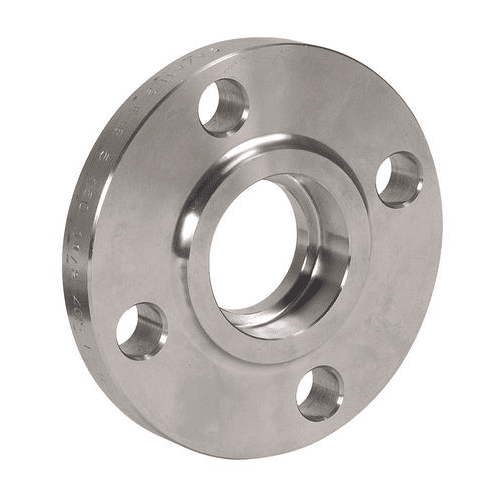
- Welded directly onto the pipe.
- The socket provides a recess to hold the pipe, allowing for a smooth flow of fluid.
- Suitable for applications with lower pressures and temperatures.
Threaded Flange
- Has internal threads and screws onto the pipe with external threads.
- Used in low-pressure, non-critical applications.
- Common in smaller pipe sizes.
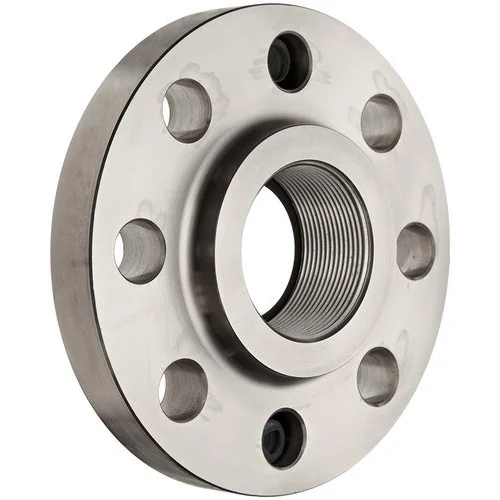
Lap Joint Flange (LJ)
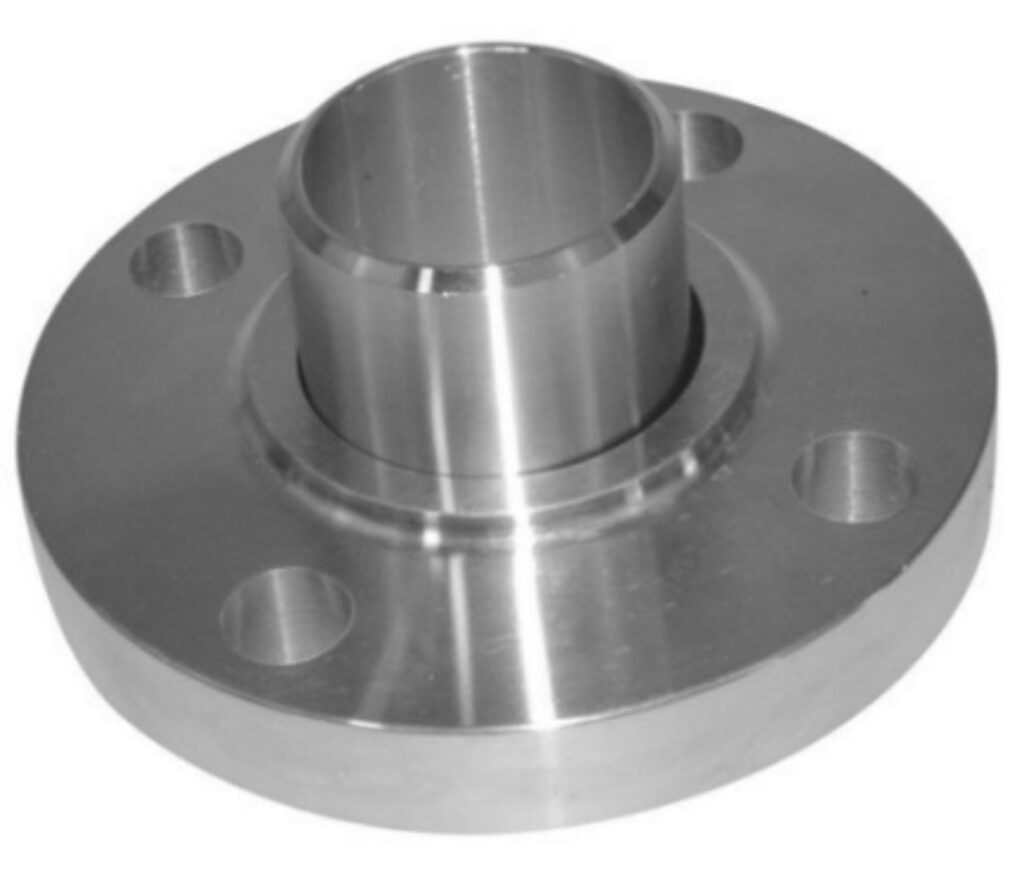
- Consists of two parts: a stub end and a loose backing flange.
- The two components are connected with bolts.
- Allows for easy alignment and adjustment during installation.
Orifice Flange (OF)
- Specifically designed for use with orifice meters to measure the flow rate of fluids.
- Has a concentric hole to accommodate the orifice meter.
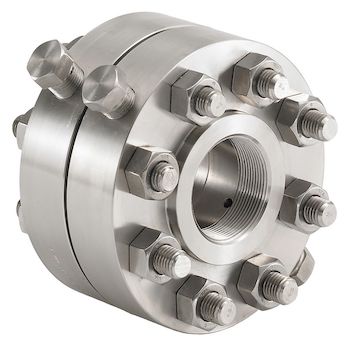
Expander Flange
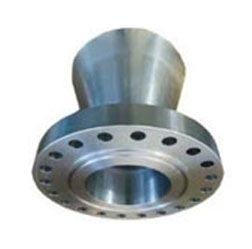
- Used in applications where an increase in pipe size is required.
- The larger end of the flange accommodates the larger pipe, while the smaller end connects to the existing pipe.
Reducing Flange
- Connects pipes of different sizes.
- The flange has a larger bore on one side and a smaller bore on the other.
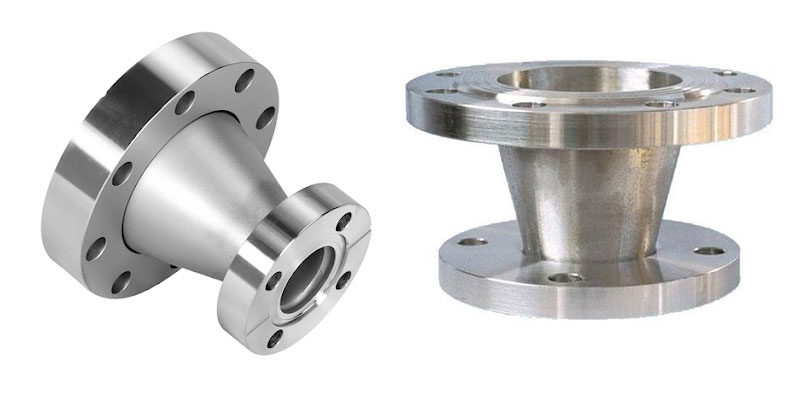
Ring Type Joint Flange (RTJ)
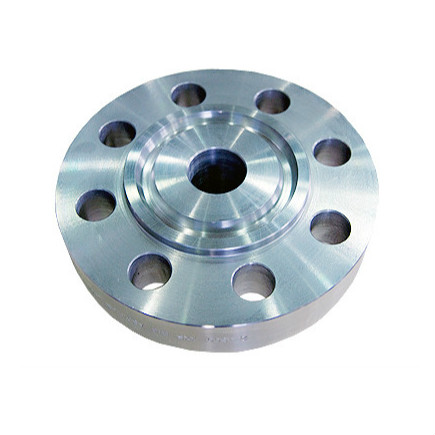
- Features a groove to accommodate a metal ring gasket.
- Suitable for high-pressure and high-temperature applications.
- Commonly used in the oil and gas industry.
Long Weld Neck Flange (LWN)
- Similar to weld neck flanges but with an extended neck.
- Provides additional reinforcement and is often used in high-pressure applications.

Square Flange

- Has a square shape rather than a circular one.
- Used in specialized applications where square-shaped connections are required.
Spacer Flange
- Used to increase the distance between two flanges in a piping system.
- Helpful in applications where additional space is needed.
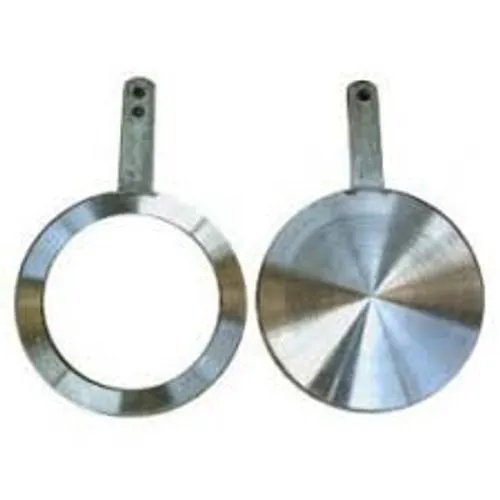
- Raised Face (RF): A common facing type where the flange face is raised above the bolting circle, providing a surface for the gasket to seat.
- Flat Face (FF): In flat-faced flanges, the flange face is flat, and gaskets are placed between the two flat faces.
- Ring Type Joint (RTJ): RTJ flanges use a metal ring gasket, creating a tight seal under high pressure.
Standards used in SS Flanges
Stainless steel flanges are critical components in piping systems, and various standards govern their design, dimensions, and materials to ensure consistency, safety, and interchangeability. Some of the key standards used for stainless steel flanges include:
- ASME B16.5:
- Pipe Flanges and Flanged Fittings NPS 1/2 through NPS 24 Metric/Inch Standard.
- This standard, published by the American Society of Mechanical Engineers (ASME), covers the dimensions and pressure-temperature ratings of flanges from NPS 1/2 to NPS 24. It includes various classes, such as 150, 300, 600, and so on, indicating pressure ratings.
- ASTM A182/A182M:
- Standard Specification for Forged or Rolled Alloy and Stainless Steel Pipe Flanges, Forged Fittings, and Valves and Parts for High-Temperature Service.
- ASTM A182 specifies the chemical composition, mechanical properties, and heat treatment requirements for forged or rolled alloy and stainless steel flanges, fittings, valves, and parts used in high-temperature service.
- ASTM A240/A240M:
- Standard Specification for Chromium and Chromium-Nickel Stainless Steel Plate, Sheet, and Strip for Pressure Vessels and for General Applications.
- ASTM A240 outlines the requirements for stainless steel plate, sheet, and strip used in pressure vessels and general applications. Flanges are often manufactured using materials that comply with A240 standards.
- ANSI/ASME B16.47:
- Large Diameter Steel Flanges NPS 26 Through NPS 60 Metric/Inch Standard.
- This standard, also developed by ASME, covers large-diameter flanges from NPS 26 to NPS 60. It includes series A and series B flanges with different dimensions and pressure ratings.
- EN 1092-1:
- Flanges and their joints – Circular flanges for pipes, valves, fittings, and accessories, PN designated – Part 1: Steel flanges.
- This European standard specifies the requirements for circular steel flanges in various pressure classes (PN designations) and includes dimensions, tolerances, and materials.
- ISO 7005-1:
- Metallic flanges – Part 1: Steel flanges.
- This International Organization for Standardization (ISO) standard provides specifications for steel flanges used in various industries. It includes dimensions, tolerances, and technical requirements.
- MSS SP-44:
- Steel Pipeline Flanges.
- Published by the Manufacturers Standardization Society (MSS), SP-44 covers steel pipeline flanges and flanged fittings with rating class designations 75, 150, 300, 400, 600, and 900.
When selecting stainless steel flanges, it’s crucial to consider the specific standards that apply to your application, as they provide guidelines for material selection, dimensions, and performance characteristics. Manufacturers and users alike reference these standards to ensure compatibility and compliance with industry requirements.
Applications of SS Flanges
Flanges are versatile components used in various industries and applications to connect pipes, valves, pumps, and other equipment in a piping system. Their primary function is to provide a secure and leak-resistant connection. Here are some common applications of flanges:
- Oil and Gas Industry:
- Flanges are extensively used in oil and gas pipelines for connecting pipes, valves, and other components.
- They play a crucial role in facilitating the assembly and maintenance of complex pipeline systems.
- Chemical Processing Industry:
- Chemical plants use flanges to connect pipes carrying corrosive chemicals and fluids.
- Flanges made from corrosion-resistant materials, such as stainless steel, are preferred in chemical processing applications.
- Petrochemical Industry:
- Flanges are employed in petrochemical facilities for connecting pipes and equipment handling petrochemical products.
- Various types of flanges are used to accommodate different pressure and temperature requirements.
- Power Generation:
- In power plants, flanges are used to connect pipes and components in steam, water, and gas systems.
- Flanges help maintain the integrity of piping systems under high temperatures and pressures.
- Water Treatment Plants:
- Water treatment facilities utilize flanges to connect pipes and equipment involved in the treatment and distribution of water.
- Flanges ensure a secure and leak-proof connection in water supply systems.
- Shipbuilding and Marine Industry:
- Flanges are widely used in shipbuilding for connecting pipes and components in various marine systems.
- They are crucial for maintaining the integrity of fluid systems on ships.
- Food and Beverage Industry:
- In the food and beverage sector, flanges are employed in piping systems for the transportation of liquids and gases.
- Stainless steel flanges are commonly used due to their corrosion resistance and hygienic properties.
- Aerospace Industry:
- Flanges are utilized in aerospace applications for connecting pipes and components in fluid and fuel systems.
- Lightweight and high-strength materials are often preferred in aerospace flange applications.
- HVAC Systems:
- Heating, ventilation, and air conditioning (HVAC) systems use flanges to connect pipes and ducts for the distribution of air and fluids.
- Flanges ensure a secure and efficient connection in HVAC systems.
- Mining Industry:
- Mining operations use flanges in piping systems for transporting minerals, slurries, and other materials.
- Heavy-duty flanges are often required to withstand the abrasive nature of mining applications.
- Construction Industry:
- In construction projects, flanges are used in plumbing and heating systems to connect pipes and components.
- Flanges contribute to the structural integrity of building systems.
- Renewable Energy:
- Flanges are employed in renewable energy projects, such as connecting pipes in geothermal and solar thermal systems.
- They contribute to the efficiency and reliability of renewable energy installations.
- Fire Protection Systems:
- Fire protection systems use flanges to connect pipes carrying water or firefighting agents.
- Flanges play a crucial role in maintaining the reliability of fire suppression systems.
Flanges come in various types, materials, and configurations to suit the specific requirements of different industries. Their widespread use in diverse applications highlights their importance in ensuring the functionality, safety, and efficiency of piping systems across various sectors.