Contact : +91-79045 61980 | Email: hydrofitengineers@gmail.com
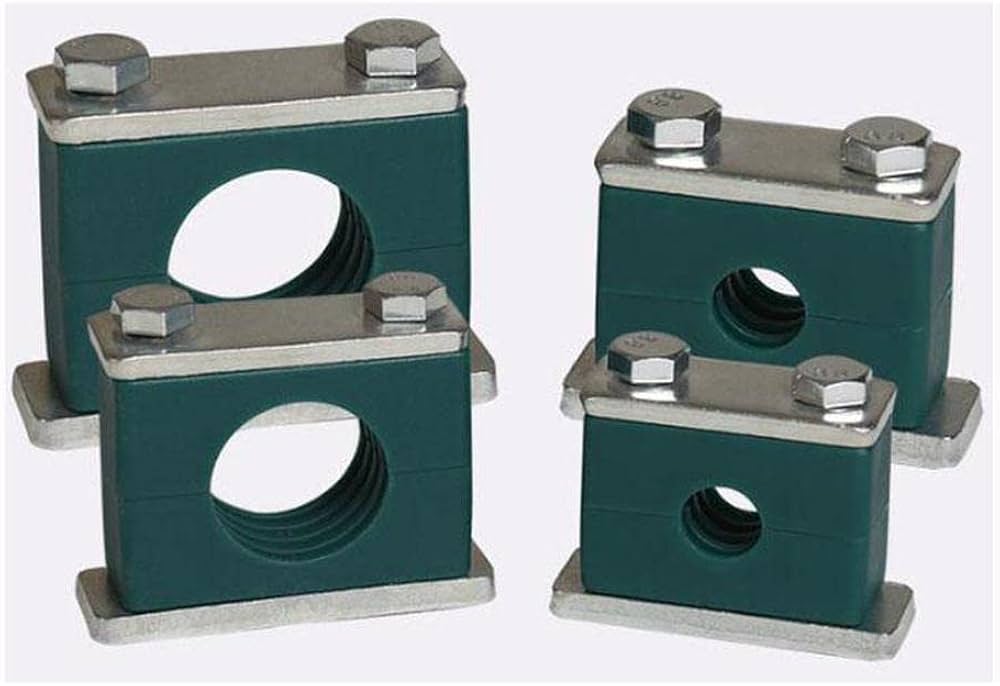
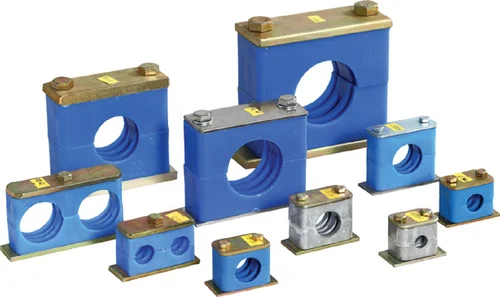
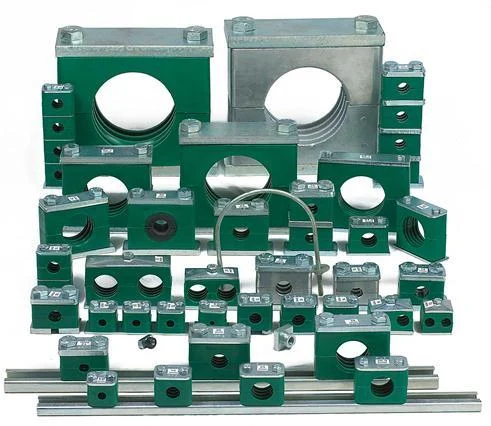
HYDRAULIC PIPE CLAMPS
Hydraulic clamps, also known as hydraulic tube clamps or hydraulic pipe clamps, are devices used to secure and support hydraulic pipes, tubes, or hoses in various applications. They are designed to provide stability and prevent movement or vibration of the pipes, which is crucial in hydraulic systems to maintain efficiency and prevent damage.
These clamps typically consist of two main parts: a metal clamp body and a securing mechanism such as bolts or screws. The clamp body is usually made of materials like steel or aluminum and is designed to securely hold the hydraulic pipe in place. The securing mechanism allows for easy installation and adjustment of the clamp to accommodate different pipe sizes.
Hydraulic clamps come in various sizes and configurations to fit different pipe diameters and mounting requirements. They are often used in industries such as manufacturing, construction, agriculture, and automotive to secure hydraulic lines in hydraulic systems, hydraulic machinery, and hydraulic power units.
Design principles of hydraulic clamps
The design principles of hydraulic pipe clamps are primarily focused on ensuring secure and stable fixation of hydraulic pipes while also providing ease of installation, maintenance, and adjustment.
- Material Selection: Hydraulic pipe clamps are typically constructed from durable materials such as steel, aluminum, or stainless steel. These materials offer strength and corrosion resistance, ensuring the longevity and reliability of the clamps in various environmental conditions.
- Clamp Design: The clamp body is designed to securely hold the hydraulic pipe in place without causing damage or deformation to the pipe. It often features a split or two-piece design, allowing for easy installation and adjustment without the need to disassemble the entire clamp.
- Mounting Options: The clamps are designed to accommodate different mounting configurations, including bolt-on, weld-on, or rail-mount designs. This versatility allows for flexibility in installation and ensures compatibility with various hydraulic system setups.
- Adjustability: Many hydraulic clamps feature adjustable components such as bolts, screws, or sliding mechanisms, allowing for easy adaptation to different pipe diameters and configurations. This adjustability ensures a secure and snug fit for the hydraulic pipe, minimizing movement and vibration.
- Cushioning: Some clamps include cushioning materials such as rubber or polyurethane inserts to provide additional support and vibration dampening. These cushions help protect the hydraulic pipe from damage caused by vibration or friction and enhance overall system performance.
- Corrosion Protection: To enhance durability and longevity, these clamps may incorporate coatings or finishes such as powder coating or zinc plating to protect against corrosion and rust, especially in harsh environments.
- Load Capacity: The design of these clamps takes into account the maximum load and pressure requirements of the hydraulic system to ensure that the clamp can withstand the forces exerted during operation without failure or deformation.
- Compliance with Standards: Design principles for hydraulic pipe clamps often adhere to industry standards and regulations to ensure product quality, safety, and compatibility with hydraulic system components.
Material of construction used in Hydraulic clamps
Hydraulic pipe clamps are typically constructed from durable materials chosen for their strength, corrosion resistance, and suitability for the intended application. The most common materials of construction used in these clamps include:
- Steel: Steel is a popular choice for hydraulic pipe clamps due to its strength and durability. Carbon steel is commonly used for standard applications, while stainless steel is preferred for environments where corrosion resistance is crucial, such as marine or chemical industries.
- Aluminum: Aluminum offers a lightweight alternative to steel while still providing adequate strength and corrosion resistance. It is often used in applications where weight reduction is a priority or in environments where steel may be prone to corrosion.
- Polypropylene (PP): Polypropylene is a thermoplastic material known for its chemical resistance and low moisture absorption. It is often used in hydraulic pipe clamps for applications where corrosion from chemicals or exposure to moisture is a concern.
- Polyamide (Nylon): Nylon is another thermoplastic material commonly used in hydraulic pipe clamps due to its high strength, durability, and resistance to abrasion. It is often reinforced with glass fibers or other additives to enhance its mechanical properties.
- Rubber: Rubber is used as a cushioning material in hydraulic pipe clamps to provide vibration dampening and protect the hydraulic pipe from damage. It is typically incorporated as an insert or coating within the clamp design.
- Stainless Steel: In addition to carbon steel, stainless steel is also used in hydraulic pipe clamps for its superior corrosion resistance, especially in harsh or corrosive environments. It is often preferred for applications where durability and longevity are paramount.
The choice of material depends on various factors such as the specific application, environmental conditions, load requirements, and budget considerations. Manufacturers may offer hydraulic pipe clamps in different material options to meet the diverse needs of their customers
Types of Hydraulic Clamps
Hydraulic pipe clamps come in various types and varieties to accommodate different pipe sizes, mounting options, and application requirements. These are some common types of hydraulic pipe clamps:
- Standard Pipe Clamps: These are the most basic type of hydraulic pipe clamps and are designed to securely hold hydraulic pipes in place. They typically consist of a metal clamp body with a bolt or screw for tightening around the pipe. Standard pipe clamps are available in various sizes to accommodate different pipe diameters.
- Heavy-Duty Pipe Clamps: Heavy-duty pipe clamps are designed to provide extra strength and support for larger or heavier hydraulic pipes. They feature a robust construction with thicker materials and reinforced components to withstand higher loads and pressures.
- Twin Pipe Clamps: Twin pipe clamps are designed to secure two parallel hydraulic pipes simultaneously. They feature a dual-clamp design with two separate clamping points, allowing for efficient installation and secure fixation of multiple pipes in close proximity.
- Cushioned Pipe Clamps: Cushioned pipe clamps incorporate rubber or polyurethane inserts to provide cushioning and vibration dampening for the hydraulic pipe. This helps reduce noise and vibration in the hydraulic system and protects the pipe from damage caused by movement or friction.
- Rail Mount Pipe Clamps: Rail mount pipe clamps are designed to be mounted on standard rail profiles, such as DIN rails or strut channels. They provide a convenient and versatile mounting solution for hydraulic pipes in industrial or construction applications.
- Welding Pipe Clamps: Welding pipe clamps are designed to be welded directly onto structural members or surfaces, providing a permanent and secure mounting solution for hydraulic pipes in custom or specialized applications.
- Split Pipe Clamps: Split pipe clamps feature a two-piece design that allows for easy installation and removal of the clamp without the need to disassemble the entire assembly. They are often used in applications where frequent maintenance or access to the hydraulic pipe is required.
- Pipe Clamp Accessories: Various accessories are available to complement hydraulic pipe clamps, including mounting brackets, extension pieces, angle adapters, and pipe support blocks. These accessories help customize the installation and provide additional support or flexibility as needed.
These are just a few examples of the types and varieties of hydraulic pipe clamps available. The specific type of clamp used will depend on factors such as the size and configuration of the hydraulic pipes, the mounting requirements, and the operating conditions of the hydraulic system.
Design features of hydraulic clamps
The design features of hydraulic pipe clamps are essential for ensuring secure and reliable fixation of hydraulic pipes while also providing ease of installation, maintenance, and adjustment. Here are some key design features commonly found in hydraulic pipe clamps
- Clamp Body Design: The clamp body is typically designed to securely hold the hydraulic pipe in place without causing damage or deformation to the pipe. It may feature a split or two-piece design to allow for easy installation and adjustment without the need to disassemble the entire clamp.
- Mounting Options: Hydraulic pipe clamps are designed to accommodate various mounting options, including bolt-on, weld-on, rail-mount, or adhesive-mount configurations. This versatility allows for flexible installation on different surfaces or structural members.
- Adjustability: Many hydraulic pipe clamps feature adjustable components such as bolts, screws, or sliding mechanisms. This allows for easy adaptation to different pipe diameters and configurations, ensuring a secure and snug fit for the hydraulic pipe.
- Cushioning: Some hydraulic pipe clamps incorporate cushioning materials such as rubber or polyurethane inserts. These cushions provide vibration dampening and protect the hydraulic pipe from damage caused by movement or friction.
- Corrosion Resistance: Hydraulic pipe clamps are often constructed from materials such as steel, aluminum, or thermoplastics that offer resistance to corrosion. Additionally, they may feature coatings or finishes such as powder coating or zinc plating to further enhance corrosion resistance.
- Load Capacity: The design of hydraulic pipe clamps takes into account the maximum load and pressure requirements of the hydraulic system. The clamp is engineered to withstand the forces exerted during operation without failure or deformation.
- Compliance with Standards: Hydraulic pipe clamps are designed to comply with industry standards and regulations to ensure product quality, safety, and compatibility with hydraulic system components. This may include standards such as DIN 3015, which specifies requirements for hydraulic pipe clamps.
- Modularity: Some hydraulic pipe clamp systems are designed with modular components that allow for easy customization and expansion of the system. This modularity enables users to configure the clamp system to meet their specific application requirements.
- Quick Release Mechanisms: Certain hydraulic pipe clamps feature quick-release mechanisms that allow for rapid installation and removal of the clamp without the need for tools. This feature is particularly useful in applications where frequent maintenance or access to the hydraulic pipe is required.
- Temperature Resistance: Hydraulic pipe clamps are designed to withstand a wide range of temperatures, ensuring reliable performance in both hot and cold environments.
By incorporating these design features, hydraulic pipe clamps provide secure and efficient support for hydraulic pipes, contributing to the overall reliability and longevity of hydraulic systems
Installation of Hydraulic Clamps
- Select the Right Clamp: Choose a hydraulic pipe clamp that is suitable for the pipe size, mounting option, and application requirements.
- Prepare the Surface: Ensure that the surface where the clamp will be mounted is clean, flat, and free of any debris or contaminants.
- Positioning: Position the hydraulic pipe clamp at the desired location along the pipe, ensuring proper alignment and clearance.
- Mounting: Depending on the type of clamp, use the appropriate mounting method (e.g., bolt-on, weld-on, rail-mount). Follow the manufacturer’s instructions for tightening bolts or welding the clamp securely in place.
- Adjustment: If the clamp is adjustable, adjust it to fit the pipe snugly without causing deformation or constriction.
- Check Alignment: Verify that the hydraulic pipe is aligned properly within the clamp and that there are no obstructions or interference with other components.
- Torque Specifications: Use the recommended torque specifications for tightening bolts or screws to prevent over-tightening or under-tightening.
- Test: After installation, perform a visual inspection and test the hydraulic system to ensure that the pipe clamp is securely holding the pipe in place and that there are no leaks or issues with pipe movement.
Maintenance of Hydraulic Clamps
- Regular Inspection: Periodically inspect hydraulic pipe clamps for signs of wear, damage, or corrosion. Look for loose bolts, cracks, deformation, or deterioration of cushioning materials.
- Tighten Loose Fasteners: If any bolts or screws are loose, tighten them to the manufacturer’s specifications to prevent movement or failure of the clamp.
- Replace Damaged Components: If any components of the hydraulic pipe clamp are damaged or worn, such as cushioning inserts or mounting hardware, replace them promptly to maintain proper functionality and support.
- Check Alignment: Ensure that the hydraulic pipe remains properly aligned within the clamp and that there are no issues with clearance or interference with other system components.
- Inspect for Leaks: Check for any signs of hydraulic fluid leaks around the pipe clamp or connections. Address any leaks immediately to prevent fluid loss and system contamination.
- Cleanliness: Keep hydraulic pipe clamps clean and free of debris or contaminants that could affect their performance or cause damage over time.
- Follow Manufacturer’s Recommendations: Adhere to the manufacturer’s recommendations for maintenance intervals and procedures to ensure optimal performance and longevity of hydraulic pipe clamps.
By following these guidelines for installation and maintenance, you can ensure that hydraulic pipe clamps provide reliable support and stability for hydraulic pipes in your system, minimizing the risk of damage or failure.
Applications of Hydraulic Clamps
Hydraulic pipe clamps find applications across various industries where hydraulic systems are utilized. Some common applications include:
- Manufacturing: Hydraulic pipe clamps are used in manufacturing processes such as machine tools, injection molding machines, presses, and automated assembly lines. They secure hydraulic pipes in place, ensuring smooth operation of hydraulic actuators and cylinders.
- Construction: In the construction industry, hydraulic pipe clamps are used in heavy equipment such as excavators, bulldozers, cranes, and forklifts. They secure hydraulic lines in place, preventing damage or interference during operation.
- Agriculture: Hydraulic pipe clamps are widely used in agricultural machinery such as tractors, combines, and harvesters. They secure hydraulic pipes in hydraulic systems used for lifting, steering, and controlling various agricultural implements.
- Automotive: In the automotive industry, hydraulic pipe clamps are used in vehicles for various applications, including power steering systems, hydraulic brakes, suspension systems, and transmission systems. They ensure secure mounting of hydraulic lines, preventing leaks or damage that could affect vehicle performance.
- Marine: In marine applications, hydraulic pipe clamps are used in vessels such as ships, boats, and offshore platforms. They secure hydraulic pipes in hydraulic systems used for steering, propulsion, winches, cranes, and other marine equipment.
- Aerospace: Hydraulic pipe clamps are used in aircraft and aerospace applications for hydraulic systems used in landing gear, flight control surfaces, braking systems, and cargo handling equipment. They ensure secure mounting of hydraulic pipes in the demanding aerospace environment.
- Oil and Gas: In the oil and gas industry, hydraulic pipe clamps are used in hydraulic systems for drilling rigs, production platforms, and pipeline operations. They secure hydraulic pipes in place, ensuring reliable operation of critical equipment in harsh and challenging environments.
- Mining: Hydraulic pipe clamps are used in mining equipment such as excavators, loaders, and haul trucks. They secure hydraulic lines in hydraulic systems used for lifting, propulsion, and material handling in mining operations.
- Material Handling: Hydraulic pipe clamps are used in material handling equipment such as conveyor systems, palletizers, and robotic arms. They secure hydraulic pipes in place, ensuring precise control and movement of materials in manufacturing and distribution facilities.
These are just a few examples of the wide range of applications where hydraulic pipe clamps are used. They play a crucial role in ensuring the reliable and efficient operation of hydraulic systems across various industries
Benefits of Hydraulic clamps
Hydraulic pipe clamps offer several benefits, but there are also considerations to keep in mind when selecting and using them
- Secure Fixation: Hydraulic pipe clamps provide a secure and stable means of fixing hydraulic pipes in place, preventing movement or vibration that could lead to damage or inefficiency in the hydraulic system.
- Vibration Dampening: Many hydraulic pipe clamps feature cushioning materials such as rubber or polyurethane inserts, which help absorb vibrations and reduce noise generated by hydraulic systems, improving overall comfort and safety.
- Damage Prevention: By securely holding hydraulic pipes in place, pipe clamps help prevent damage to pipes, fittings, and other system components caused by movement, vibration, or external impacts, thus extending the lifespan of the hydraulic system.
- Easy Installation and Adjustment: Hydraulic pipe clamps are designed for easy installation and adjustment, allowing for quick and hassle-free setup of hydraulic piping systems. This facilitates maintenance and modifications as needed.
- Compatibility: Hydraulic pipe clamps are available in various sizes, configurations, and mounting options, making them compatible with a wide range of hydraulic pipes, fittings, and system components.
- Versatility: Hydraulic pipe clamps can be used in diverse applications across industries such as manufacturing, construction, agriculture, automotive, marine, and aerospace, offering versatility and flexibility in hydraulic system design and installation.
- Corrosion Resistance: Many hydraulic pipe clamps are constructed from materials such as stainless steel or corrosion-resistant coatings, ensuring durability and longevity even in harsh operating environments.
Considerations of Hydraulic Clamps
- Proper Sizing: It’s essential to select the correct size and type of hydraulic pipe clamp to ensure a secure fit for the specific pipe diameter and application requirements. Using improperly sized clamps can lead to instability and potential damage to the hydraulic system.
- Load Capacity: Consider the maximum load and pressure requirements of the hydraulic system when selecting hydraulic pipe clamps to ensure that they can withstand the forces exerted during operation without failure or deformation.
- Environmental Factors: Take into account environmental factors such as temperature, humidity, exposure to chemicals, and UV radiation when choosing hydraulic pipe clamps. Select materials and coatings that offer suitable resistance to these environmental conditions to prevent premature wear or corrosion.
- Maintenance: Regular inspection and maintenance of hydraulic pipe clamps are necessary to ensure optimal performance and longevity of the hydraulic system. Check for signs of wear, damage, or corrosion and replace any worn or damaged components promptly.
- Installation: Proper installation of hydraulic pipe clamps is crucial for their effectiveness and reliability. Follow manufacturer guidelines and torque specifications when installing clamps to avoid over-tightening or under-tightening, which can compromise their performance.
By considering these factors and leveraging the benefits of hydraulic pipe clamps, one can ensure the efficient and reliable operation of hydraulic systems in various industrial applications.
Safety Considerations of Hydraulic Clamps
Safety considerations when working with hydraulic pipe clamps are essential to prevent accidents, injuries, and damage to equipment. Here are some key safety considerations:
- Proper Installation: Ensure that hydraulic pipe clamps are installed correctly according to manufacturer guidelines and industry standards. Improper installation can lead to instability, leaks, or failure of the hydraulic system.
- Secure Mounting: Use appropriate mounting methods and hardware to secure hydraulic pipe clamps in place. Make sure that clamps are tightly fastened to prevent movement or dislodgement during operation.
- Inspect Regularly: Perform regular inspections of hydraulic pipe clamps to check for signs of wear, damage, or corrosion. Look for loose bolts, cracks, deformation, or deterioration of cushioning materials. Replace any worn or damaged components promptly.
- Avoid Overloading: Consider the maximum load and pressure ratings of hydraulic pipe clamps when designing and operating hydraulic systems. Avoid overloading clamps beyond their specified capacity, as this can lead to failure or deformation.
- Use Proper Tools and Equipment: Use appropriate tools and equipment for installation, maintenance, and repair of hydraulic pipe clamps. Follow safety procedures and wear personal protective equipment (PPE) such as gloves and safety glasses when working with hydraulic systems.
- Prevent Fluid Leaks: Check hydraulic pipe clamps regularly for signs of fluid leaks around connections or fittings. Address any leaks immediately to prevent fluid loss, contamination, and safety hazards.
- Bleed Pressure: Before performing maintenance or repair on hydraulic systems, ensure that pressure is relieved from the system and that hydraulic fluid is fully bled to prevent accidental activation of hydraulic components.
- Follow Lockout/Tagout Procedures: When servicing hydraulic systems, follow lockout/tagout procedures to ensure that energy sources are isolated and equipment is safely de-energized to prevent accidental startup or movement.
- Training and Education: Ensure that personnel working with hydraulic pipe clamps are adequately trained and knowledgeable about proper installation, maintenance, and safety procedures. Provide ongoing training and education to keep employees informed about best practices and safety guidelines.
- Emergency Response: Have emergency response procedures in place in case of accidents, spills, or injuries related to hydraulic systems. Provide access to first aid kits, emergency eyewash stations, and other safety equipment as needed.
By prioritizing safety and adhering to these considerations, one can minimize the risk of accidents and ensure the safe operation of hydraulic systems involving pipe clamps