Contact : +91-79045 61980 | Email: hydrofitengineers@gmail.com
Oil Level Indicator - Fluid Level Gauge
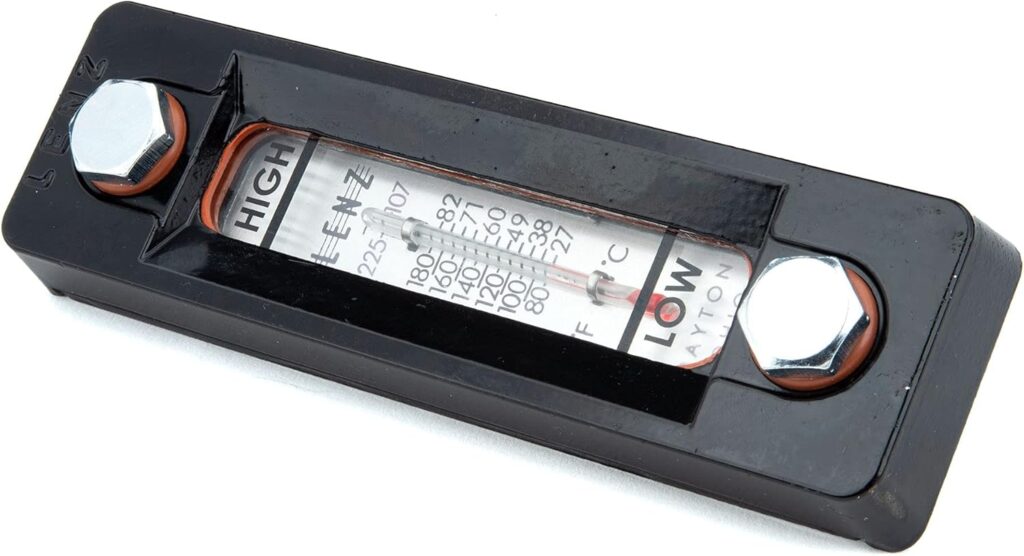
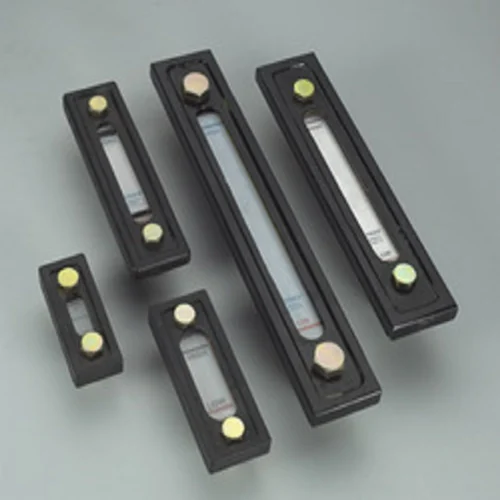
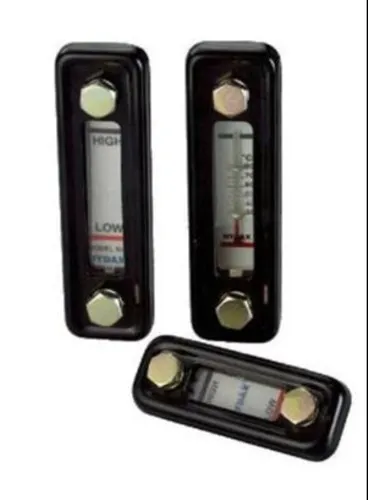
An oil level indicator for hydraulics is a device that is used to measure the oil level in hydraulic systems. The gauge typically consists of a clear tube or sight glass that is installed in the hydraulic system, allowing the operator to visually inspect the oil level.
The fluid oil level indicator is an important component of a hydraulic system because it allows the operator to monitor the oil level and ensure that the system is properly lubricated. If the oil level is too low, it can cause damage to the hydraulic system components or lead to system failure. Conversely, if the oil level is too high, it can cause foaming or overheating of the oil, which can also damage the system.
Fluid oil level indicator gauges can be designed to work with a variety of hydraulic fluids, including mineral oils, synthetic fluids, and water-based fluids. They are typically made from materials that are resistant to corrosion and wear, such as aluminum, brass, or stainless steel.
In addition to visual sight gauges, there are also electronic oil level sensors that can be used to measure oil levels in hydraulic systems. These sensors typically use a float or probe that is submerged in the oil and sends a signal to a digital display or monitoring system.
Types of Oil Level Indicators
- Mechanical Indicators:
- Sight Glass: A transparent tube or window on the side of the reservoir, allowing visual inspection of the oil level.
- Float Gauges: These use a float connected to an indicator that moves with the oil level.
- Dipsticks: A rod marked with level indicators that can be inserted into the reservoir to check the oil level manually.
- Electrical/Electronic Indicators:
- Capacitive Sensors: Measure changes in capacitance caused by the presence or absence of oil.
- Ultrasonic Sensors: Use sound waves to detect the oil level.
- Resistive Sensors: Measure the resistance, which changes with the level of oil.
Features and Benefits
- Accuracy: Precise measurement of oil levels to ensure optimal operation.
- Real-Time Monitoring: Continuous monitoring and instant feedback.
- Alarms and Alerts: Can trigger alarms or alerts if oil levels drop too low or rise too high.
- Remote Monitoring: Some systems allow for remote monitoring and data logging.
Installation and Maintenance
- Placement: Typically installed on the side of the hydraulic reservoir.
- Calibration: Regular calibration may be necessary to maintain accuracy.
- Cleaning: Ensure the sight glass or sensors are clean for accurate readings.
- Inspection: Regularly check for wear and tear, and replace components as needed.
Applications of Hydraulic Fluid Level Gauges
- Industrial Machinery: Used in manufacturing and production equipment.
- Mobile Equipment: Found in construction, agricultural, and mining machinery.
- Automotive Systems: Used in power steering and other hydraulic applications in vehicles.
Importance of Hydraulic Fluid Level Gauges
Maintaining the correct oil level in a hydraulic system is essential for:
- Preventing Cavitation: Low oil levels can cause air to enter the system, leading to cavitation and damage.
- Ensuring Lubrication: Adequate oil levels ensure that all components are properly lubricated.
- Temperature Control: Oil helps in dissipating heat, and the correct level is vital for effective cooling.
- System Efficiency: Proper oil levels contribute to the overall efficiency and longevity of the hydraulic system.
Design Considerations of Hydraulic Fluid Level Gauges
- System Requirements:
- Reservoir Size and Shape: The design of the gauge should match the dimensions and shape of the hydraulic reservoir.
- Operating Environment: Consider the operating temperature, pressure, and exposure to contaminants.
- Measurement Range: Determine the minimum and maximum oil levels that need to be measured.
- Type of Gauge:
- Mechanical: Sight glass, float gauges, dipsticks.
- Electrical/Electronic: Capacitive, ultrasonic, resistive sensors.
- Materials:
- Corrosion Resistance: Use materials that resist corrosion from hydraulic oil and environmental factors.
- Durability: Ensure the materials can withstand mechanical stresses and temperature variations.
There are basically two types of Hydraulic Level Gauges
- Mechanical Gauges
- Electronic Gauges
Mechanical Gauges
Sight Glass
- Design:
- A transparent tube or window that allows visual inspection of the oil level.
- Markings on the glass to indicate different oil levels.
- Construction:
- Materials: Typically made from borosilicate glass or polycarbonate for clarity and durability.
- Mounting: Secured to the side of the reservoir using threaded fittings or flanges.
- Seals: Use O-rings or gaskets to prevent leaks.
Float Gauges
- Design:
- A float connected to an indicator that moves with the oil level.
- The float should be buoyant and move freely with changing oil levels.
- Construction:
- Float: Made from materials like stainless steel or plastic.
- Indicator: Attached to the float via a rod or cable, with a pointer or dial showing the oil level.
- Housing: Protects the moving parts and mounts to the reservoir.
Electronic Gauges
Capacitive Sensors
- Design:
- Measure changes in capacitance caused by the presence or absence of oil.
- Construction:
- Sensor: Consists of two conductive plates or a rod and the reservoir wall acting as the other plate.
- Electronics: Circuitry to convert capacitance changes into readable signals.
- Housing: Protects the sensor and electronics, typically made from corrosion-resistant materials.
Ultrasonic Sensors
- Design:
- Use sound waves to detect the oil level.
- Construction:
- Transducer: Emits and receives ultrasonic signals.
- Controller: Processes the signals and converts them into level readings.
- Mounting: Attached to the top or side of the reservoir.
Manufacturing Process of Level Gauges
- Prototyping:
- Create prototypes of the gauge designs.
- Test the prototypes in simulated operating conditions.
- Material Selection:
- Choose materials based on durability, resistance to hydraulic oil, and environmental conditions.
- Fabrication:
- Use machining, molding, or assembly processes to create the components.
- Assemble the components into the final gauge design.
- Testing:
- Test the gauges for accuracy, reliability, and durability.
- Conduct pressure and leak tests to ensure integrity.
- Calibration:
- Calibrate the gauges to ensure accurate readings across the intended measurement range.
- Quality Control:
- Implement quality control procedures to check for defects and ensure consistency in production.
Hydraulic Fluid Level Gauge - SG Series
The Hydraulic fluid level gauge SG series is a type of fluid level gauge designed specifically for hydraulic systems. It is typically used to measure the oil level in hydraulic reservoirs or tanks.
The SG series fluid level gauge typically consists of a clear plastic or glass sight tube that is mounted on the outside of the hydraulic tank. The tube is filled with hydraulic fluid and has markings on it to indicate the fluid level. The fluid level can be easily read by looking through the sight tube.
The SG series fluid level gauge is designed to be durable and resistant to the harsh operating conditions of hydraulic systems. It is typically made from materials such as brass or aluminum, which are resistant to corrosion and wear.
One advantage of the SG series fluid level gauge is that it allows the operator to quickly and easily check the oil level in the hydraulic system without the need for special tools or equipment. This can help to prevent damage to the system by ensuring that it is properly lubricated.
Overall, the SG series fluid level gauge is a simple and effective tool for monitoring the oil level in hydraulic systems. It is widely used in a variety of industrial applications, including construction equipment, agricultural machinery, and manufacturing equipment.
These gauges are available in lengths of 3″, 5″, 7″, 9″ and 11″ lengths
Two prominent manufacturers who make SG Series Oil Level Gauges are HYDAX and HYDROLINE
At Hydrofit Engineers these Fluid Level or Oil Level Gauges are available from ex-stock with all the sizes ranging from 3″ to 11″ available in stock in sufficient quantities.