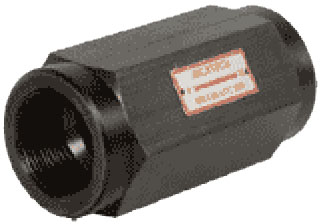
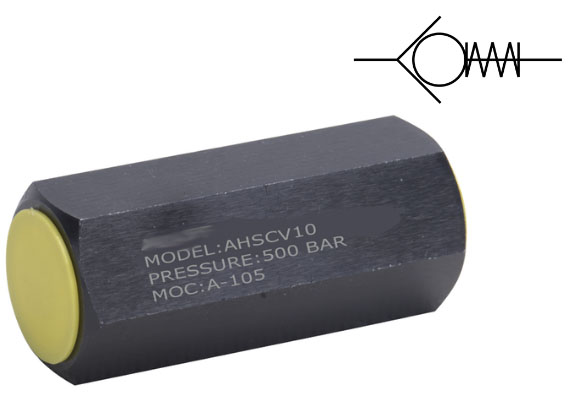
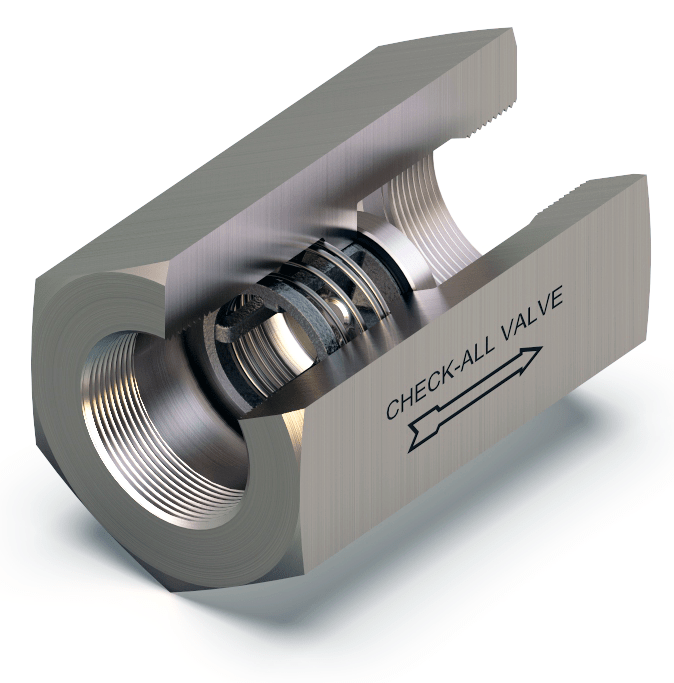
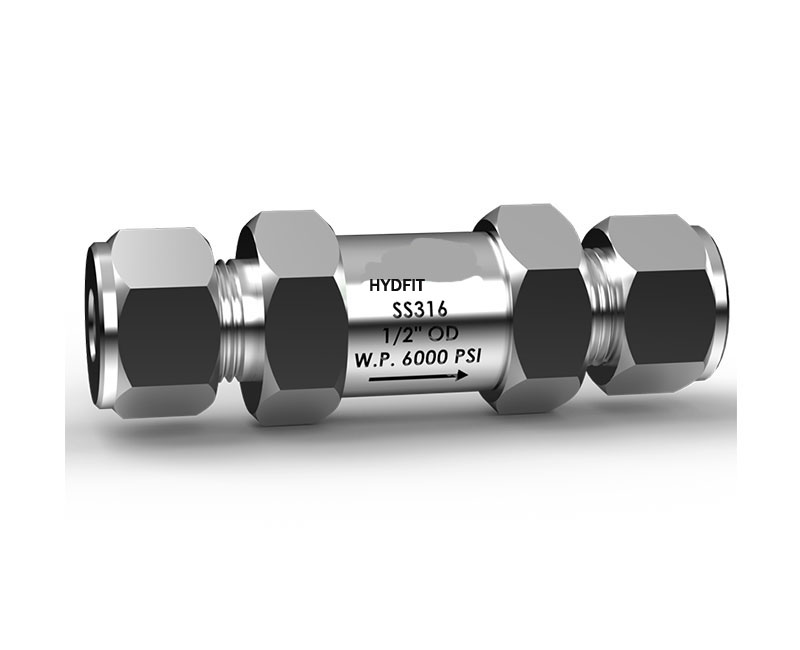
Hydraulic systems are fundamental in a wide array of industries, ranging from manufacturing and construction to aerospace and automotive. One of the crucial components that ensure the smooth operation of these systems is the hydraulic check valve. These valves play a critical role in controlling the flow of fluid, preventing backflow, and ensuring that hydraulic systems function safely and efficiently. This article provides an in-depth look at hydraulic check valves, exploring their function, types, applications, and benefits.
Table of Contents
ToggleWhat is a Hydraulic Check Valve ?
A hydraulic check valve is a mechanical device designed to allow fluid (usually oil or hydraulic fluid) to flow through it in one direction only. Its primary function is to prevent the reverse flow of fluid within a hydraulic system, which can lead to system inefficiency, damage, or failure. Check valves are essential in maintaining pressure, protecting pumps and other components, and ensuring the smooth operation of the entire hydraulic system.
How Does a Hydraulic Check Valve work ?
The operation of a hydraulic check valve is relatively simple yet highly effective. The valve is typically composed of an inlet port, an outlet port, and a movable element (such as a ball, disc, or piston) that controls the flow of fluid. When fluid flows in the desired direction, it pushes the movable element, opening the valve and allowing the fluid to pass through. If the fluid attempts to flow in the opposite direction, the movable element is pushed back against a sealing surface, closing the valve and preventing reverse flow.
The ability of the check valve to prevent backflow is critical in maintaining the integrity of the hydraulic system. Backflow can cause pressure drops, lead to pump cavitation, and result in damage to sensitive components. By preventing this, check valves help to prolong the life of the system and maintain its efficiency.
Types of Hydraulic Check Valves
Hydraulic check valves come in various types, each designed to meet specific requirements and applications. The most common types include:
- Ball Check Valves
Ball check valves are among the simplest and most widely used types of hydraulic check valves. They consist of a ball that sits on a sealing seat. When fluid flows in the correct direction, the ball is pushed off the seat, allowing fluid to pass through. If the flow reverses, the ball is pushed back onto the seat, sealing the valve and preventing backflow. Ball check valves are durable, reliable, and suitable for a wide range of applications.
- Poppet Check Valves
Poppet check valves use a poppet (a type of movable element) to control the flow of fluid. The poppet is spring-loaded and rests against a sealing surface. When fluid flows in the desired direction, it overcomes the spring force, pushing the poppet away from the seat and allowing fluid to pass through. If the flow reverses, the spring forces the poppet back onto the seat, sealing the valve. Poppet check valves are known for their fast response time and are often used in high-pressure applications.
- Disc Check Valves
Disc check valves use a flat disc as the movable element. The disc is hinged or spring-loaded and sits on a sealing seat. When fluid flows in the correct direction, the disc is lifted off the seat, allowing fluid to pass. If the flow reverses, the disc is pushed back onto the seat, sealing the valve. Disc check valves are commonly used in applications where a large flow rate is required.
- Swing Check Valves
Swing check valves use a swinging disc or gate that pivots on a hinge. When fluid flows in the correct direction, the disc swings open, allowing fluid to pass through. If the flow reverses, the disc swings back against the seat, sealing the valve and preventing backflow. Swing check valves are often used in applications with low-pressure systems and large-diameter pipes.
- Pilot-Operated Check Valves
Pilot-operated check valves are more complex than the other types mentioned above. They combine the functions of a check valve and a directional control valve. These valves are designed to allow fluid flow in one direction and can be opened in the opposite direction when a pilot pressure is applied. This type of check valve is used in applications where controlled reverse flow is required, such as in hydraulic cylinders.
Applications of Hydraulic Check valves
Hydraulic check valves are used across various industries and applications due to their critical role in maintaining the proper flow of hydraulic fluid. Some common applications include:
- Hydraulic Cylinders
Check valves are used in hydraulic cylinders to maintain pressure and prevent the reverse flow of fluid, ensuring that the cylinder extends and retracts smoothly. In applications such as lifting equipment and construction machinery, check valves are vital in maintaining the stability and safety of the system.
- Pumps and Motors
In hydraulic pumps and motors, check valves prevent backflow that could lead to cavitation, reduce efficiency, or damage the equipment. By ensuring that fluid flows in the correct direction, check valves help maintain the longevity and performance of these critical components.
- Hydraulic Presses
Hydraulic presses rely on check valves to maintain pressure during the pressing operation. The valves prevent fluid from flowing back into the pump, ensuring that the press maintains the required force throughout the process.
- Aerospace and Automotive Systems
In aerospace and automotive systems, hydraulic check valves are used to control fluid flow in braking, steering, and other critical systems. These valves help maintain safety and performance by preventing backflow and ensuring that hydraulic pressure is maintained.
Benefits of Using Hydraulic Check Valves
The use of hydraulic check valves offers several key benefits, including:
- Preventing Backflow: The primary function of check valves is to prevent backflow, which is essential in maintaining system efficiency and preventing damage to components.
- Maintaining Pressure: Check valves help maintain pressure in hydraulic systems, ensuring that the system operates smoothly and efficiently.
- Protecting Equipment: By preventing reverse flow and pressure drops, check valves protect pumps, motors, and other sensitive components from damage.
- Enhancing Safety: In applications where hydraulic systems are critical to safety, such as in aerospace and construction, check valves play a vital role in ensuring the system’s reliability and stability
Hydraulic check valves are indispensable components in hydraulic systems, providing essential functions such as preventing backflow, maintaining pressure, and protecting equipment. With various types available, including ball, poppet, disc, swing, and pilot-operated check valves, these devices can be tailored to meet the specific needs of different applications. Whether in industrial machinery, aerospace, automotive systems, or hydraulic presses, check valves play a critical role in ensuring the smooth and efficient operation of hydraulic systems. Their ability to enhance safety, protect equipment, and maintain system integrity makes them a vital part of any hydraulic system.
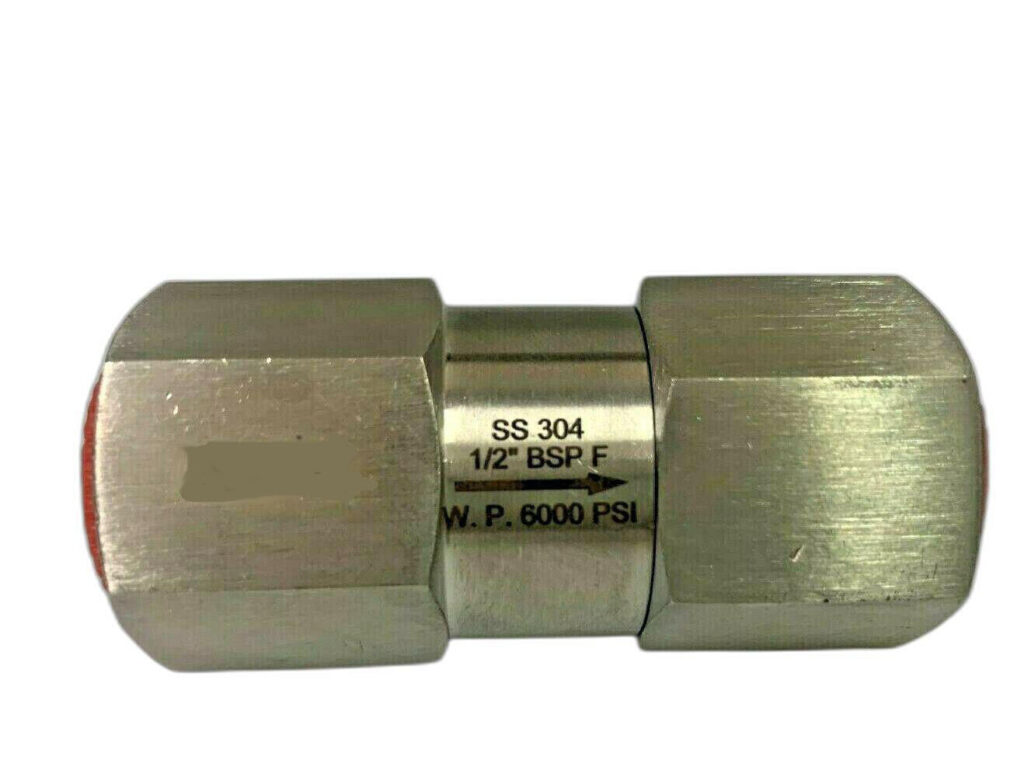
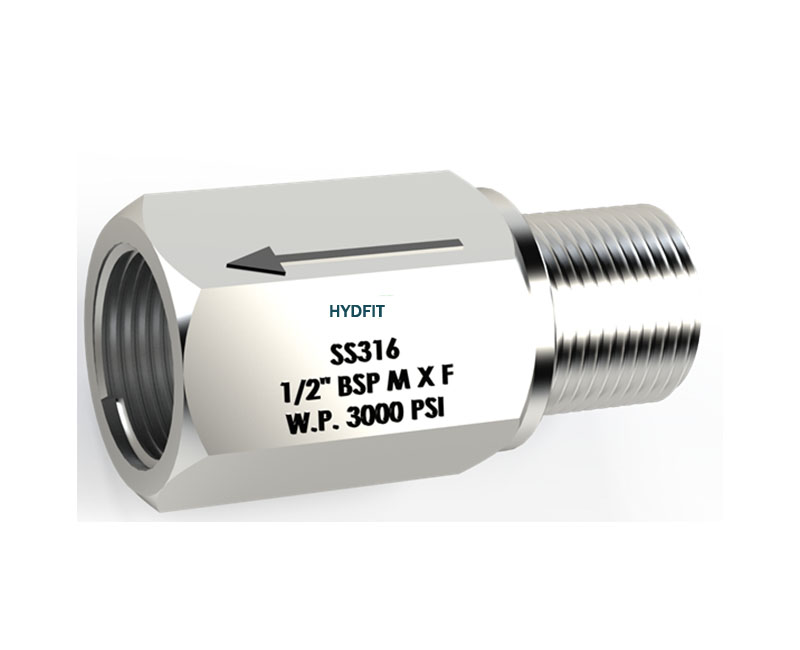