Contact : +91-79045 61980 | Email: hydrofitengineers@gmail.com
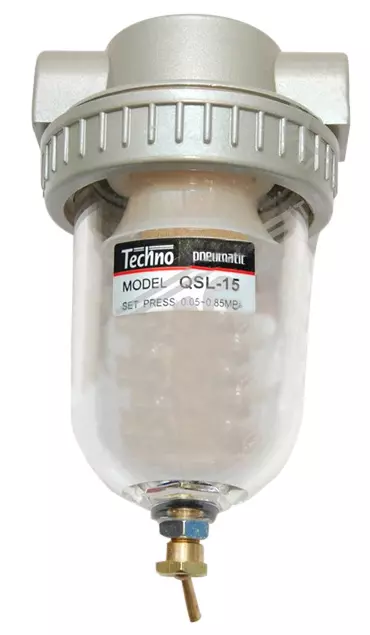
Pneumatic Air Filters
Pneumatic air filters are designed to remove contaminants from compressed air, ensuring that only clean air flows through the system. These contaminants can include dust, dirt, oil, water vapor, and other particulate matter. By removing these impurities, air filters prevent damage to sensitive pneumatic components such as valves, cylinders, and actuators.
Types Of Pneumatic Air Filters
- Particulate Filters: Particulate filters are the most common type of pneumatic air filters. They utilize a porous filtering material, such as paper or synthetic fibers, to trap solid particles from the compressed air stream. These filters are effective at removing dust, dirt, and other solid contaminants.
- Coalescing Filters: Coalescing filters are specialized filters designed to remove liquid contaminants, such as oil and water, from the compressed air. They use a unique filtration mechanism to capture tiny droplets of liquid and coalesce them into larger droplets that can be drained away. Coalescing filters are essential for applications where clean, dry air is critical, such as in precision manufacturing or laboratory settings.
- Activated Carbon Filters: Activated carbon filters are used to remove odors, vapors, and other gaseous contaminants from the compressed air. These filters contain activated carbon, which has a high surface area and adsorptive properties. As air passes through the filter, odorous or harmful gases are trapped by the activated carbon, resulting in cleaner air.
- Combination Filters: Combination filters combine multiple filtration mechanisms into a single unit, offering comprehensive protection against various types of contaminants. These filters typically integrate particulate, coalescing, and activated carbon filtration stages to provide high-quality compressed air.
Importance of Pneumatic Air Filters
- Protection of Pneumatic Components: Pneumatic air filters safeguard sensitive pneumatic components from damage caused by contaminants. By ensuring clean air supply, filters prevent clogging, wear, and malfunction of valves, cylinders, and other components.
- Improved System Reliability: Clean air provided by pneumatic filters enhances the reliability and efficiency of pneumatic systems. Consistent air quality prevents unexpected downtime and costly repairs, resulting in increased productivity and profitability.
- Enhanced Product Quality: In applications where air quality directly affects product quality, such as in food processing or pharmaceutical manufacturing, pneumatic air filters play a crucial role. By removing contaminants, filters help maintain product integrity and meet quality standards.
Worker Safety: Clean air is essential for ensuring a safe working environment for personnel. Pneumatic air filters help reduce exposure to harmful contaminants and airborne particles, protecting the health and well-being of workers
Operation of Pneumatic Air Filters
Entrance of Compressed Air: The compressed air, which may contain contaminants such as dust, dirt, oil droplets, and water vapor, enters the pneumatic air filter from the compressor or storage tank.
Filtration Process: Inside the air filter housing, the compressed air passes through a filter element or cartridge. This filter element is typically made of porous material, such as paper, felt, or synthetic fibers, with varying levels of filtration efficiency.
Contaminant Separation: As the compressed air flows through the filter element, contaminants are physically captured and separated from the air stream. Larger particles like dust and dirt are trapped on the surface of the filter, while smaller particles like oil mist and water vapor are captured within the filter media.
Coalescing Action: In addition to mechanical filtration, some pneumatic air filters feature a coalescing element. This element promotes the coalescence of fine oil mist and water droplets into larger droplets, making them easier to capture and remove from the air stream.
Clean Air Outlet: The filtered and purified air exits the air filter through the outlet port. The contaminants that have been captured by the filter element are prevented from re-entering the pneumatic system, ensuring that only clean and dry air is delivered to downstream components and devices.
Drainage: In pneumatic systems where liquid contaminants such as oil and water are present, air filters may include a drainage mechanism to remove accumulated liquids from the filter housing. This prevents the buildup of liquids that could potentially impair the performance of the filter and downstream pneumatic equipment.
Maintenance: Periodic maintenance of pneumatic air filters is essential to ensure their continued effectiveness. Depending on the application and operating conditions, the filter element may need to be replaced or cleaned regularly to maintain optimal filtration efficiency.
Overall, the working principle of pneumatic air filters involves the filtration and separation of contaminants from the compressed air stream to provide clean, dry, and high-quality air for pneumatic systems. By removing harmful particles and liquids, pneumatic air filters help protect downstream components, extend equipment lifespan, and ensure reliable operation of pneumatic machinery and devices.
Hydrofit Engineers offers Pneumatic Air Filters of sizes from 1/4″ BSP to 2″ BSP in different models for different conditions. Most of the all filters come with a metal gaurd to safegaurd the Polycarbonate Bowl of the Filter. However, some brands may not offer the bowl gaurd by default.
TECHNO JELPC SPAC JANATICS FESTO