Contact : +91-79045 61980 | Email: hydrofitengineers@gmail.com
HYDRAULIC PROPORTIONAL VALVE
Proportional valves are a type of hydraulic or pneumatic valve that allows for precise control over the flow rate, pressure, or direction of fluid within a system. Unlike conventional on/off valves, proportional valves offer variable control, meaning they can adjust the flow or pressure in proportion to an input signal
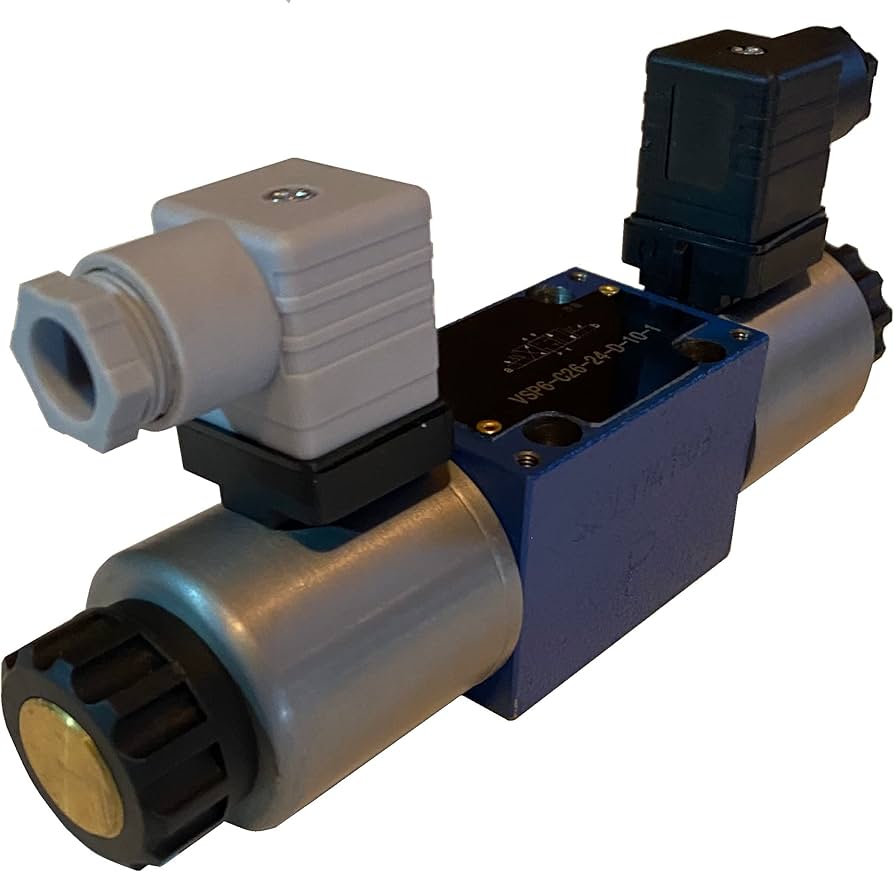
These valves are a type of hydraulic or pneumatic valve that allows for precise control over the flow rate, pressure, or direction of fluid within a system. Unlike conventional on/off valves, proportional valves offer variable control, meaning they can adjust the flow or pressure in proportion to an input signal
How Proportional Valves typically work
Control Signal Input
Proportional valves receive an electrical, pneumatic, or hydraulic control signal that specifies the desired flow rate, pressure, or position. This signal is typically provided by a control system such as a PLC (Programmable Logic Controller), PID controller, or manual input device.
Variable Opening
Based on the input signal, the valve adjusts the size of its opening or the position of its internal components to regulate the flow of fluid through the valve. This adjustment can be linear or nonlinear, depending on the valve design and application requirements
Proportional Control
The flow rate, pressure, or direction of fluid through the valve is directly proportional to the input signal. For example, increasing the input signal will result in a corresponding increase in flow rate, pressure, or valve opening, and vice versa
Feedback Control
Many of these valves incorporate feedback mechanisms, such as position sensors or pressure transducers, to provide closed-loop control and ensure accurate and stable operation. Feedback signals are compared to the input signal to adjust the valve position or opening as needed to maintain the desired output
These valves operate on the principle of modulating the flow or pressure of hydraulic fluid in proportion to an input signal
- Input Signal: These valves receive an input signal from an external control system, such as a PLC (Programmable Logic Controller), PID controller, or manual input device. This signal specifies the desired flow rate, pressure, or position of the valve.
- Control Electronics: The input signal is processed by control electronics within the proportional valve. These electronics typically include amplifiers, feedback circuits, and control algorithms. The electronics determine the appropriate position or opening of the valve to achieve the desired output based on the input signal and feedback from sensors.
- Solenoid or Servo Control: Depending on the type of proportional valve, the control electronics actuate a solenoid or servo mechanism to adjust the position of the valve’s internal components. Solenoid-operated proportional valves use electrical signals to control the movement of a magnetic coil, which in turn adjusts the position of the valve spool or other actuating elements. Servo-operated proportional valves use hydraulic pressure to control the movement of a servo piston, which directly positions the valve spool or other actuating elements.
- Variable Flow or Pressure Regulation: As the position of the valve’s internal components changes in response to the input signal, the flow rate or pressure of hydraulic fluid passing through the valve is modulated accordingly. Proportional valves can regulate flow or pressure in a linear or nonlinear manner, depending on the valve design and application requirements.
- Feedback Control: Many hydraulic proportional valves incorporate feedback mechanisms, such as position sensors or pressure transducers, to provide closed-loop control. Feedback signals from these sensors are compared to the input signal to ensure accurate and stable operation of the valve. Any deviations between the desired output and actual output are corrected by adjusting the position or opening of the valve’s internal components.
- Output Signal: The output signal from the proportional valve, which represents the regulated flow rate or pressure of hydraulic fluid, is sent to the actuator or hydraulic circuit being controlled. The actuator responds to the regulated flow or pressure to perform the desired mechanical function, such as moving a hydraulic cylinder or controlling the speed of a hydraulic motor.
Overall, hydraulic proportional valves provide precise and responsive control over the flow or pressure of hydraulic fluid, making them valuable components in a wide range of hydraulic systems requiring accurate and dynamic control.
Functioning and Operation of Hydraulic Proportion Valve
The functioning and operation of a hydraulic proportional valve involve several key steps, from receiving an input signal to modulating the flow or pressure of hydraulic fluid
Input Signal
Hydraulic proportional-valves receive an input signal from an external control system, such as a PLC (Programmable Logic Controller), PID controller, or manual input device. This signal specifies the desired flow rate, pressure, or position of the valve
Control Electronics
The input signal is processed by the control electronics integrated into the proportional-valve. These electronics typically include amplifiers, feedback circuits, and control algorithms. They analyze the input signal and determine the appropriate position or opening of the valve to achieve the desired output.
Actuation Mechanism
Depending on the type of proportional valve, the control electronics actuate a solenoid or servo mechanism to adjust the position of the valve’s internal components
- Solenoid-Operated Valve: Solenoid-operated proportional-valves use electrical signals to control the movement of a magnetic coil. This coil exerts a force on the valve spool, which adjusts the flow area within the valve
- Servo-Operated Valve: Servo-operated proportional valves use hydraulic pressure to control the movement of a servo piston. The position of this piston directly positions the valve spool, adjusting the flow area within the valve
Variable Flow or Pressure Regulation
As the position of the valve’s internal components changes in response to the input signal, the flow rate or pressure of hydraulic fluid passing through the valve is modulated accordingly. This modulation can be linear or nonlinear, depending on the valve design and application requirements
Feedback Control
Many of these valves incorporate feedback mechanisms, such as position sensors or pressure transducers. These sensors provide real-time feedback on the actual position or pressure of the valve. The feedback signals are compared to the input signal to ensure accurate and stable operation
Output Signal
The output signal from the proportional valve represents the regulated flow rate or pressure of hydraulic fluid. This signal is sent to the actuator or hydraulic circuit being controlled. The actuator responds to the regulated flow or pressure to perform the desired mechanical function, such as moving a hydraulic cylinder or controlling the speed of a hydraulic motor
Throughout this process, the proportional-valve continuously adjusts its position or opening to maintain the desired flow rate or pressure, providing precise and dynamic control over the hydraulic system. This enables a wide range of applications requiring accurate fluid control, such as machine tools, industrial automation, and mobile machinery
Advantages of Proportional Valves
Hydraulic proportional valves offer several advantages compared to conventional on/off valves or other types of control valves. Here are some key advantages:
- Precise Control: These provide precise control over the flow rate, pressure, or position of hydraulic fluid within a system. This level of control allows for accurate and finely-tuned adjustments to meet specific application requirements.
- Variable Operation: Unlike on/off valves that only provide two states (fully open or fully closed), proportional valves offer variable operation. They can modulate the flow or pressure of hydraulic fluid in proportion to an input signal, allowing for smooth and continuous adjustment of system parameters.
- Dynamic Response: Proportional valves can respond rapidly to changes in input signals, making them suitable for applications requiring dynamic control. They can adjust flow rates or pressure levels in real-time to accommodate variations in system conditions or external demands.
- Energy Efficiency: By precisely controlling the flow of hydraulic fluid, proportional valves can help optimize energy usage within hydraulic systems. They reduce energy consumption by avoiding excessive flow rates or pressure levels, leading to improved overall system efficiency.
- Reduced Wear and Tear: Proportional valves operate smoothly and with minimal pressure surges, resulting in reduced wear and tear on system components such as pumps, actuators, and pipelines. This extends the lifespan of hydraulic equipment and reduces maintenance costs over time.
- Flexibility: Hydraulic proportional valves are versatile and can be used in a wide range of applications across various industries. They can control different types of hydraulic actuators, such as cylinders, motors, and directional control valves, making them suitable for diverse hydraulic system configurations.
- Improved Performance: The precise control offered by proportional valves enhances the performance of hydraulic systems. It allows for smoother operation, greater accuracy in positioning or speed control, and better overall system performance in terms of productivity, accuracy, and reliability.
- Safety: Proportional valves contribute to improved safety in hydraulic systems by enabling accurate and responsive control over critical parameters such as pressure, flow, and actuator positioning. This helps prevent equipment damage, reduce the risk of accidents, and enhance operator safety.
- Integration with Automation Systems: Proportional valves can be easily integrated into automation systems, allowing for seamless communication and coordination with other components and devices. This facilitates the implementation of sophisticated control strategies and enhances the overall efficiency and productivity of automated processes.
Overall, hydraulic proportional valves offer significant advantages in terms of precision, flexibility, energy efficiency, and performance, making them valuable components in a wide range of hydraulic systems and applications
Applications of Hydraulic Proportional Valves
Hydraulic proportional valves find extensive applications across various industries where precise control over fluid flow, pressure, or direction is required. Here are some common applications:
- Machine Tools: Proportional valves are used in machine tool applications such as CNC (Computer Numerical Control) machining centers, lathes, milling machines, and grinding machines. They control the flow and pressure of hydraulic fluid to actuate tool movements, clamping mechanisms, and other machine functions with high precision.
- Injection Molding: Hydraulic proportional valves are essential components in injection molding machines used for manufacturing plastic parts. They regulate the flow and pressure of hydraulic fluid to control the movement of injection units, mold clamping systems, and screw drives, ensuring accurate and repeatable molding processes.
- Industrial Automation: Proportional valves play a crucial role in various industrial automation applications, including packaging machinery, material handling systems, and assembly lines. They control the movement of actuators, conveyor belts, robotic arms, and other equipment, enabling precise positioning, speed control, and synchronization of operations.
- Mobile Equipment: Hydraulic proportional valves are widely used in mobile machinery such as excavators, loaders, cranes, and forestry equipment. They regulate the flow and pressure of hydraulic fluid to control the movement of hydraulic cylinders, motors, and directional control valves, facilitating smooth and efficient operation of mobile equipment in diverse working conditions.
- Aerospace and Defense: Proportional valves are employed in aircraft and military systems for various functions, including flight control surfaces, landing gear actuation, weapon systems, and auxiliary equipment. They provide precise control over hydraulic actuators, ensuring safe and reliable operation of critical aircraft and defense systems.
- Marine and Offshore: Hydraulic proportional valves are used in marine vessels, offshore platforms, and subsea equipment for tasks such as steering, propulsion, winching, and cargo handling. They control the movement of hydraulic cylinders, motors, and winches, enabling efficient and reliable operation in marine and offshore environments.
- Process Control: Proportional valves play a key role in process control applications across industries such as chemical processing, oil and gas, and water treatment. They regulate the flow, pressure, and temperature of liquids and gases in valves, pumps, and control systems, ensuring precise control over industrial processes and optimizing production efficiency.
- Test and Simulation: Proportional valves are used in test rigs and simulation systems for automotive, aerospace, and other applications. They control the flow and pressure of hydraulic fluid to simulate real-world conditions and test the performance of components, systems, and vehicles under different operating scenarios.
These are just a few examples of the diverse applications of hydraulic proportional valves across different industries. Their ability to provide precise and dynamic control over hydraulic systems makes them indispensable components in a wide range of industrial, commercial, and mobile applications.
Proportional Valves from ARGO HYTOS