Contact : +91-79045 61980 | Email: hydrofitengineers@gmail.com
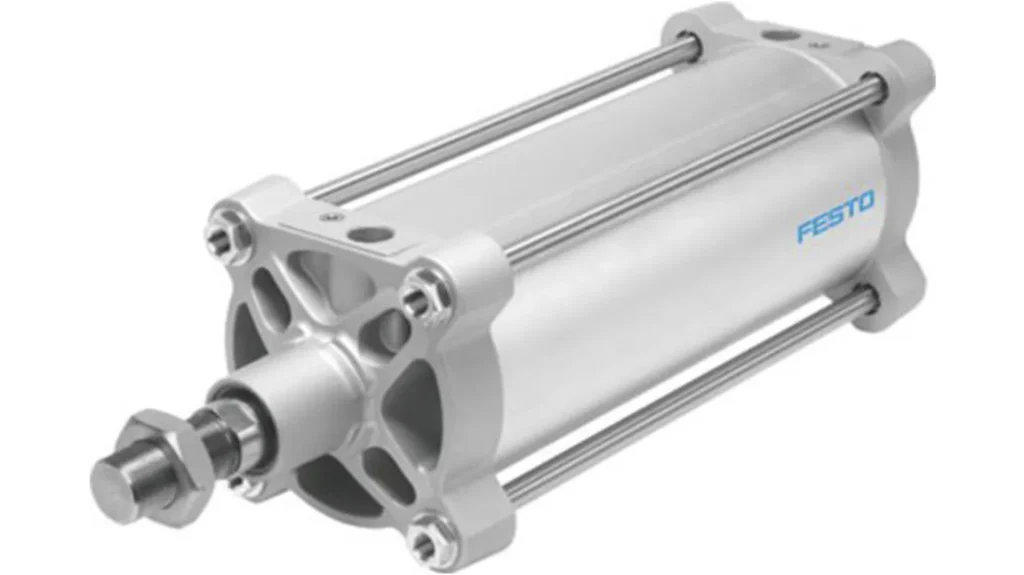
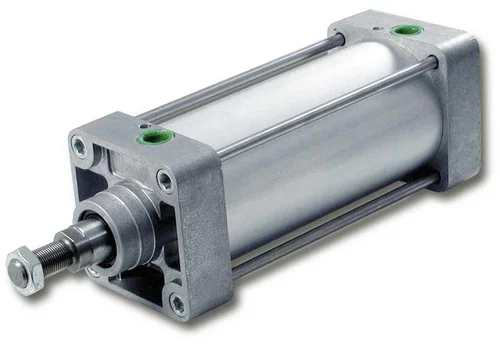
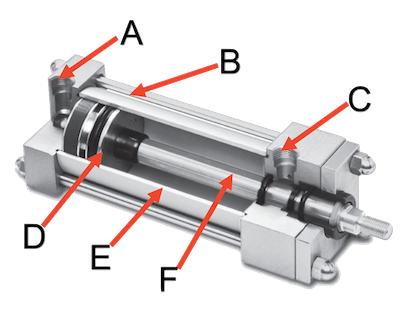
What is a Pneumatic Cylinder
A pneumatic cylinder is a mechanical device that uses the power of compressed air to produce force and motion. It is a type of linear actuator, meaning it creates motion in a straight line, as opposed to rotary motion.
The basic components of a pneumatic cylinder include a cylindrical chamber or tube, a piston, and two valves—one for intake and one for exhaust. Compressed air is introduced into the cylinder through the intake valve, causing the piston to move in the desired direction. The exhaust valve allows air to escape from the cylinder, enabling the piston to return to its original position.
Pneumatic cylinders are commonly used in various industrial applications, such as manufacturing, automation, and machinery. They are valued for their simplicity, reliability, and relatively low cost. Additionally, pneumatic systems are often preferred in environments where cleanliness and the avoidance of electrical components are important, as they do not produce sparks and are not affected by electrical interference.
Manufacturer, Dealer, Stockist and Supplier of Pneumatic Cylinders
Hydrofit Engineers is a reputed manufacturer, dealer, stockist and supplier of Pneumatic Cylinders in Chennai, Tamil Nadu located in the country of India
Working principle of a pneumatic cylinder
The working principle of a pneumatic cylinder involves the conversion of compressed air energy into mechanical motion, specifically linear motion. Here’s a step-by-step explanation of how a pneumatic cylinder operates:
- Introduction of Compressed Air: The process begins with the introduction of compressed air into the pneumatic cylinder. Compressed air is usually supplied by a pneumatic system through a valve.
- Cylinder Chamber and Piston: The pneumatic cylinder consists of a cylindrical chamber or tube with a piston fitted inside. The piston is free to move back and forth within the chamber.
- Air Inlet and Intake Valve: The compressed air is directed into the cylinder through an intake valve. The intake valve opens to allow the high-pressure air to enter the cylinder.
- Pressure Buildup: As the compressed air enters the cylinder, it creates pressure inside the chamber. The pressure acts on the piston, causing it to move in the direction determined by the design of the system.
- Linear Motion: The movement of the piston results in linear motion. The force generated by the compressed air is transmitted to any connected load or system, enabling the cylinder to perform various mechanical tasks such as lifting, pushing, or pulling.
- Exhaust Valve: Once the piston has completed its stroke, an exhaust valve opens to allow the air to escape from the cylinder. This prepares the cylinder for the next cycle.
- Return Stroke: If the application requires a return stroke, the exhaust valve allows the air to exit the cylinder, and the piston returns to its original position under the influence of external forces (e.g., spring force or load).
- Control System: The entire process is controlled by a pneumatic control system that manages the opening and closing of valves to regulate the air flow and, consequently, the movement of the piston.
In summary, a pneumatic cylinder utilizes the force generated by compressed air to produce linear motion in a controlled and predictable manner. The cycle of intake, pressure buildup, linear motion, exhaust, and return is repeated as needed for the specific application or task at hand.
Functions of a Pneumatic Cylinder
Pneumatic cylinders serve various functions in different industrial and mechanical applications. Here are some detailed functions of pneumatic cylinders:
- Linear Motion: Pneumatic cylinders provide controlled linear motion, converting the energy from compressed air into mechanical motion. This linear movement can be used to perform tasks such as lifting, pushing, pulling, clamping, and more.
- Force Generation: Pneumatic cylinders generate force by converting the potential energy stored in compressed air into kinetic energy. The force produced depends on the size of the cylinder, air pressure, and the effective area of the piston.
- Automation and Control: Pneumatic cylinders are widely used in automated systems for controlling the movement of various components. They play a crucial role in applications such as conveyor systems, packaging machinery, and assembly lines.
- Clamping and Holding: Pneumatic cylinders are employed for clamping and holding objects in place. They can exert a force to securely hold workpieces during machining or assembly processes, ensuring precision and stability.
- Feeding and Ejecting: In manufacturing and processing industries, pneumatic cylinders are used to feed materials into a process or eject finished products. They provide controlled movement for precise positioning and handling of materials.
- Sorting and Positioning: Pneumatic cylinders are used in sorting systems to push, pull, or divert items based on their characteristics. They are also crucial for precise positioning of components in various applications.
- Braking and Stopping: Pneumatic cylinders can be employed in braking systems to control the speed and stop the motion of machinery. They are often used in conjunction with other components to ensure smooth and controlled deceleration.
- Vibration Damping: In certain applications, pneumatic cylinders can be used for damping vibrations. By adjusting the air pressure and controlling the movement of the piston, they can help absorb and dissipate vibrations in mechanical systems.
- Remote Operation: Pneumatic systems, including cylinders, can be easily controlled remotely. This makes them suitable for applications where it’s important to operate machinery or perform tasks in locations that are difficult or hazardous for humans.
- Compact and Lightweight Design: Pneumatic cylinders are known for their compact and lightweight design, making them suitable for applications where space and weight constraints are crucial considerations.
- Cost-Effective Automation: Pneumatic systems, including cylinders, are generally more cost-effective than some alternative methods of automation. They are often chosen for their simplicity, ease of maintenance, and affordability.
These functions highlight the versatility and usefulness of pneumatic cylinders in a wide range of industrial and manufacturing processes.
Types of Pneumatic Cylinders
Pneumatic cylinders come in various types, each designed to suit specific applications based on factors such as force requirements, space constraints, and environmental conditions. Here are some common types of pneumatic cylinders:
- Single-Acting Cylinder:
- Working Principle: Uses compressed air to exert force in one direction (usually extension).
- Operation: Air pressure is applied to one side of the piston, and a spring or external force returns the piston to its original position.
- Double-Acting Cylinder:
- Working Principle: Uses compressed air to exert force in both directions (extension and retraction).
- Operation: Air pressure is alternately applied to either side of the piston, allowing for controlled movement in both directions.
- Tandem Cylinder:
- Design: Consists of two cylinders connected in series.
- Operation: Air pressure is applied to both cylinders simultaneously, providing increased force.
- Rotary Cylinder:
- Design: Converts pneumatic pressure into rotary motion.
- Operation: Utilizes a rotary vane mechanism or a rack-and-pinion system to produce rotational movement.
- Rodless Cylinder:
- Design: The piston is mounted externally, and the actuator is contained within a cylindrical housing.
- Advantages: Saves space and provides a longer stroke length compared to traditional cylinders.
- Telescoping Cylinder:
- Design: Consists of nested cylinders that extend and retract in a telescopic manner.
- Application: Used when a long stroke length is required without a large retracted length.
- Impact Cylinder:
- Design: Specifically designed to absorb and dampen impact forces.
- Application: Suitable for applications where the load or actuator may experience sudden impacts.
- Guided Cylinder:
- Design: Includes guidance mechanisms to prevent side loading and improve stability.
- Application: Used in applications where precise linear motion is crucial.
- Compact Cylinder:
- Design: Characterized by a smaller footprint and lightweight construction.
- Application: Ideal for applications with limited space or where weight is a critical factor.
- Cushioned Cylinder:
- Design: Features built-in cushions at the end of the stroke to reduce impact forces.
- Advantages: Enhances the cylinder’s lifespan and provides smoother operation.
It’s important to note that the availability and characteristics of pneumatic cylinders can vary among manufacturers, and new designs or variations may be introduced over time. When selecting a pneumatic cylinder, factors such as bore size, stroke length, operating pressure, and environmental conditions should be considered to ensure optimal performance in a specific application. One should always refer to the manufacturer’s specifications and guidelines for proper installation and use